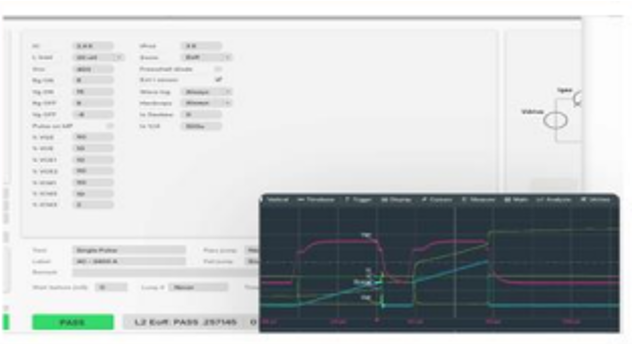
项目背景
在半导体行业的快速发展进程中,某半导体企业面临着生产过程中多个关键环节需要优化升级的挑战。随着市场对产品质量和生产效率要求的不断提高,企业原有的生产系统和技术在 IGBT(绝缘栅双极型晶体管)生产相关的自动化程序以及设备控制方面逐渐暴露出不足。具体表现为 IGBT 生产线上的操作流程缺乏高效的自动化支持,导致生产效率受限,并且在生产质量控制方面存在一定的提升空间。
项目目标
- IGBT Easiyline EAP Phase1(2018.11 - 2020.04)
- 目标是初步建立 IGBT Easiyline 生产线上的设备自动化程序(EAP),实现部分关键生产环节的自动化操作,减少人工干预,提高生产效率和产品质量的稳定性。
- IGBT Easiyline EAP Phase2(2020.06 - 至今)
- 在第一阶段的基础上,进一步完善和扩展 EAP 系统,实现 IGBT Easiyline 生产线全流程的高度自动化,优化生产节拍,降低生产成本,并提高产品的一致性和良品率。
- FDC/APC(2021.09 - 至今)
- 针对生产过程中的故障检测与分类(FDC)以及先进过程控制(APC)进行项目实施,旨在通过先进的监控和控制技术,实时监测生产过程中的异常情况,实现对生产参数的精准控制,从而进一步提升产品质量和生产效率。
应用技术
- IGBT Easiyline EAP Phase1
- 采用工业自动化编程技术,针对 IGBT Easiyline 生产线上的核心设备编写自动化控制程序。
- 运用传感器技术,对生产过程中的关键参数(如温度、压力、电流等)进行实时采集,作为自动化操作的输入数据。
- 搭建初步的数据通信网络,实现生产设备之间的数据交互,确保自动化操作的协同性。
- IGBT Easiyline EAP Phase2
- 在原有自动化程序基础上,引入先进的生产流程优化算法,根据生产线的实时状态动态调整生产节拍和设备操作顺序。
- 集成更精密的传感器和检测设备,进一步丰富生产数据的采集维度,为生产过程的精准控制提供数据支持。
- 应用智能控制系统,通过对大量生产数据的分析和学习,实现对生产过程中异常情况的自动预警和处理。
- FDC/APC
- 部署先进的故障检测与分类系统,采用机器学习算法对生产过程中的海量数据进行分析,建立故障模型,实现对潜在故障的早期检测和准确分类。
- 运用先进过程控制技术,通过实时监测生产参数,并结合反馈控制机制,对生产过程中的关键工艺参数(如蚀刻深度、掺杂浓度等)进行精准调节。
- 建立生产数据管理平台,对 FDC 和 APC 产生的数据进行存储、分析和可视化展示,以便生产管理人员及时了解生产状态并做出决策。
成果展示
- IGBT Easiyline EAP Phase1
- 成功实现了 IGBT Easiyline 生产线上关键环节的自动化操作,人工操作时间减少了约 30%。
- 通过自动化控制,生产过程中的参数波动范围缩小,产品质量的稳定性得到显著提升,产品不良率降低了约 15%。
- 初步的数据通信网络确保了设备间的协同工作,生产效率提高了约 20%。
- IGBT Easiyline EAP Phase2
- 在全流程自动化实现后,整个生产线的人工干预减少了约 70%,极大地降低了人力成本。
- 生产节拍得到优化,产品的生产周期缩短了约 30%,生产效率进一步提升了约 40%。
- 借助智能控制系统,产品的一致性得到极大改善,良品率提高了约 25%,产品在市场上的竞争力显著增强。
- FDC/APC
- 故障检测与分类系统能够提前预警约 80% 的潜在故障,并且故障分类的准确率达到了 90% 以上,有效减少了因设备故障导致的生产中断时间。
- 先进过程控制技术使关键生产参数的控制精度提高到 ±1% 以内,产品质量得到了进一步提升,产品性能的一致性得到更好的保障。
- 生产数据管理平台为生产决策提供了有力支持,管理人员能够根据实时数据及时调整生产策略,整体运营效率提高了约 30%。
通过这一系列项目的实施,该半导体企业在 IGBT 生产领域实现了从自动化到智能化的跨越,显著提升了自身的市场竞争力和生产效益。